Testimonials, case studies, and examples found on this page are results that have been forwarded to us by users of Olivine products and related products, and may not reflect the typical purchaser’s experience, may not apply to the average person and are not intended to represent or guarantee that anyone will achieve the same or similar results. is the retailer of products on this site. ® is a registered trademark of Click Sales Inc., a Delaware corporation located at 1444 S. Entertainment Ave., Suite 410 Boise, ID 83709, USA and used by permission. role as retailer does not constitute an endorsement, approval or review of these products or any claim, statement or opinion used in promotion of these products.
The website’s content and the product for sale is based upon the author’s opinion and is provided solely on an “AS IS” and “AS AVAILABLE” basis. You should do your own research and confirm the information with other sources when searching for information regarding health issues and always review the information carefully with your professional health care provider before using any of the protocols presented on this website and/or in the product sold here. Neither nor the author are engaged in rendering medical or similar professional services or advice via this website or in the product, and the information provided is not intended to replace medical advice offered by a physician or other licensed healthcare provider. You should not construe sale of this product as an endorsement by of the views expressed herein, or any warranty or guarantee of any strategy, recommendation, treatment, action, or application of advice made by the author of the product.
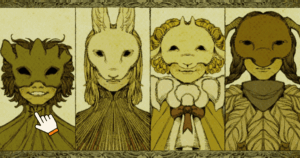
Which Yaelokre Character Are You?
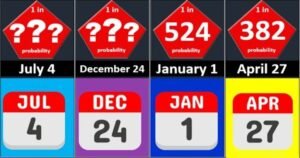
How Rare Is Your Birthday?

How Rare Is Your Name?
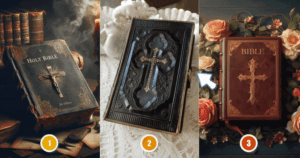
Tap The Bible To See What Does God Want To Say To You?
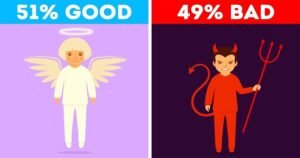
Are You Good Or Bad? Take Quiz To Find Out!
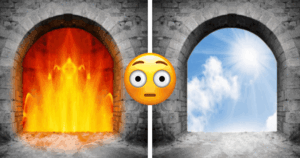
What Are Your Chances Of Going To Heaven Or Hell?
Privacy Terms & Conditions Disclaimer Contact
Copyright © 2025 All Rights Reserved.